Equipment from China for the mining industry
We offer the latest models of popular equipment for the mining industry. Our competitive prices and transparent terms are complemented by fast delivery.
Contact us to receive a free consultation.
We collaborate with the best manufacturers
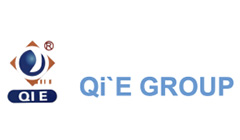
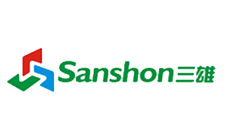
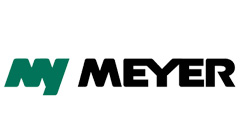

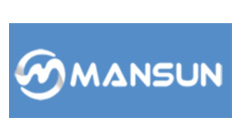
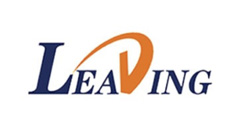
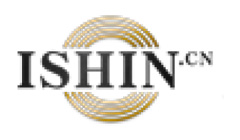
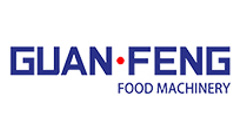
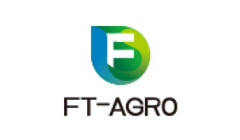
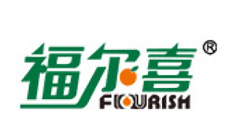


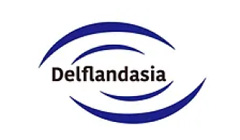

Mining operations automation is a crucial step toward enhancing safety, efficiency, and cost reduction in the mining industry.
Modern automation technologies reduce manual labor, cut operational expenses, and improve process control. One major focus area is the automation of drilling and blasting. Automated drilling rigs use computer control and positioning systems for precise drilling with minimal human involvement, while remotely operated blasting complexes perform detonations safely and reduce risks to personnel.
Transport automation also plays a vital role. Autonomous dump trucks guided by GPS and sensors lower accident rates and save fuel. Automated conveyor systems optimize material flow and reduce equipment wear during transportation in quarries and mines.
Excavation and mineral extraction benefit from robotic excavators equipped with sensors and AI for autonomous operation, and automated harvesters that adjust based on rock density to boost productivity.
Monitoring and control systems—such as ground-penetrating radar and digital twins of mines—help analyze geological conditions and forecast hazards. Safety is further enhanced by automated systems like inspection robots and gas analyzers with auto shut-off functions, providing added worker protection and accident prevention.
Overall, mining automation significantly improves the safety and productivity of extraction and excavation processes.
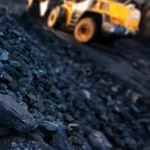
Drilling rigs play a key role in the mining industry, ensuring efficient execution of drilling operations such as exploration and production drilling. These rigs are used for extracting natural resources including coal, ore, oil, and gas, as well as for creating blast holes. Modern rigs are equipped with automated and remotely controlled mechanisms, which increase safety and productivity.
There are several types of drilling rigs, differing by drilling method and field of application. Rotary drilling rigs use the rotational motion of the drill bit to break rock and are used in geological exploration and oil and gas extraction. Percussion-rotary rigs combine rotary and percussive drilling, often with pneumatic hammers, and are used in quarries and ore mining. Auger rigs use a helical auger to lift rock and are ideal for exploration drilling. Down-the-hole pneumatic rigs operate with compressed air and are designed for hard rock, quarries, and tunnel construction.
Depending on the area of application, there are exploration, quarry, mine, and horizontal directional drilling rigs, each designed for specific working conditions. The main components of drilling rigs include the derrick, drill bit, drill rods, pneumatic hammer, circulation system, and winch. Modern rigs are equipped with automatic control systems and remote operation, improving drilling accuracy and safety.
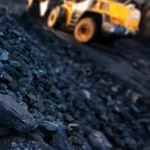
Mining machines play an important role in the extraction of minerals, construction, and other industries where complex mechanized operations are required. These machines significantly increase productivity, ensure safety, and reduce the costs of mining and processing ore, coal, and other minerals.
There are several types of mining machines, each performing its own task in the extraction process. Machines for drilling and blasting operations, such as drilling rigs and pneumatic hammers, are designed to prepare mine workings and create blast holes. They work with hard rock and are used both in open-pit mines and underground mines.
Machines for extracting minerals, such as excavators and mining combines, provide mechanized extraction of rock masses. Excavators can be hydraulic, mechanical, or walking and operate in open pits, while mining combines are underground machines designed for automated extraction of coal and ore.
Machines for transporting rock masses, such as dump trucks, conveyor systems, and monorail transport systems, allow for efficient movement of extracted materials to processing plants. There is also equipment for loading and processing, including front-end loaders, crushers, and screens, which sort and crush the rock.
Auxiliary equipment, such as mine ventilation systems and dust suppression systems, is necessary to ensure safe working conditions. Modern mining machines are often equipped with automated systems, which increases their efficiency and safety.
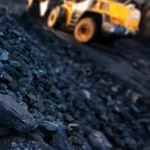
Equipment for the oil and gas industry plays a key role at all stages of extraction, processing, and transportation of hydrocarbons. Depending on working conditions (onshore or offshore fields, drilling depth, and other factors), different types of equipment are used.
Drilling equipment includes drilling rigs, which can be land-based, offshore, or flexible for operation in challenging conditions. Pumping units supply fluids to cool drilling tools and remove waste, while cementing pumps reinforce well walls.
Oil and gas extraction equipment includes submersible pumps for lifting oil from great depths, as well as rod and tubing pumps for shallower wells. Membrane and piston pumps are used for gas transfer.
Processing and purification equipment consists of separators for splitting oil, gas, and water; degassing units; and water separators that remove excess moisture from hydrocarbons.
Transportation equipment includes pipelines for long-distance transport of hydrocarbons, oil and gas pumping stations, and cargo tankers for transporting oil by sea.
Storage equipment includes oil tanks and underground gas storage facilities, which are essential for storing hydrocarbons before processing or transport.
Auxiliary equipment, such as water supply systems and gas compressors, is necessary to ensure smooth operations during extraction and processing.
The proper selection and use of such equipment is critically important for the efficient operation of the oil and gas sector, ensuring high productivity and safety.
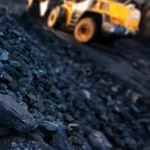
Crushers are important equipment in the mining industry, designed to break down rock and prepare materials for further processing, such as sorting and beneficiation. The main types of crushers include jaw, cone, impact (hammer), roll, and tracked crushers.
Jaw crushers are intended for primary crushing of large materials by compressing them between a fixed and a moving jaw. These machines are effective for processing hard and abrasive materials such as coal and limestone.
Cone crushers are used for secondary and tertiary processing, providing finer crushing of materials such as copper, gold, and silver.
Impact crushers operate by striking material with a rotating rotor, making them ideal for brittle materials such as gypsum and coal.
Roll crushers deliver a higher output of fine fractions by compressing material between rotating rolls and are used in the metallurgical and cement industries.
Tracked crushers are mobile machines that can operate directly at the mining site, reducing transportation costs and speeding up processing.
The choice of crusher depends on the type of material, required particle sizes, and mobility needs. It’s also important to consider supporting equipment such as conveyors, vibrating screens, and magnetic separators, which help ensure efficient processing of the crushed material.
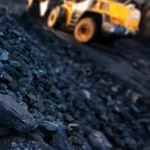
Conveyors for the mining industry are essential equipment for transporting materials such as ore, coal, and other minerals. Depending on the type of material and operating conditions, different types of conveyors are used.
Belt conveyors are the most common devices for transporting bulk materials such as coal and ore.
Scraper conveyors use metal scrapers to move heavy and dirty materials, such as coal and slurry, and can operate in conditions of high humidity and contamination.
Pipe conveyors are a type of belt conveyor used to transport dust and aggressive chemicals in closed systems.
Screw conveyors with a rotating screw effectively move viscous and bulk materials, working well in confined spaces.
Overhead conveyors are designed for transporting large and heavy materials using containers that move along an overhead system.
When selecting a conveyor for the mining industry, it is important to consider the type of material, transport distance, and operating conditions such as humidity, temperature, and contamination.
Conveyor equipment includes gearboxes, sensors, rollers, and tensioning mechanisms that ensure efficient operation and system monitoring.
The proper choice of conveyor depends on material characteristics, distance, and working conditions, allowing for efficient material transport during mining and processing.
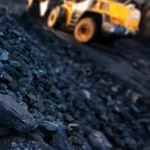
Coal mining machines play a key role in ensuring efficient and safe operation at coal deposits. Depending on the extraction method — open-pit or underground — different types of equipment are used.
Excavators are used in open-pit mines to remove coal and overburden. There are hydraulic, mechanical, walking excavators, and draglines, each differing in design and application.
For underground coal mining, mining combines with cutting drums or cutters are used. They can be rotary or shearer loaders and deliver high productivity in confined spaces.
Jackhammers are used to break hard rock manually or in hard-to-reach areas and operate on pneumatic or hydraulic drives.
Auger machines are used for drilling and extracting coal in narrow workings — the rotating auger feeds the coal onto a conveyor.
Vibratory excavators and scrapers help move coal through mines and pits using vibration and mechanical traction.
Conveyors, including belt and screw types, ensure coal is transported over various distances.
Automation, remote control, and monitoring systems increase safety and efficiency. Additional equipment such as hydraulic systems, gearboxes, feeding mechanisms, and gas analyzers ensure reliable operation.
Choosing the right equipment based on mine conditions helps increase productivity and reduce risks during coal extraction.
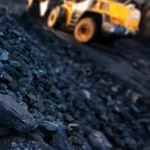
Gold mining equipment plays a key role in the efficient extraction of precious metal from ore and placer deposits. The process begins with drilling: drilling rigs create boreholes for exploration and blasting, using rotary, auger, and pneumatic machines depending on the type of rock.
Next come excavators — including hydraulic, walking, and dragline excavators — which remove overburden to access gold-bearing layers. Jaw, cone, and hammer crushers are used for primary ore crushing, preparing it for further stages.
At the concentration stage, gravity and centrifugal concentrators, ball mills, and sluice boxes are used to separate gold from lighter minerals. In areas with placer gold, wash plants, dry separators, and vibrating separators are used to efficiently extract gold without water.
When dealing with complex ores, flotation units — such as mechanical and column flotation machines — help recover gold using air bubbles and chemical reagents. The recovered gold then goes through smelting in induction furnaces, where high temperatures separate the metal from impurities.
In some cases, chemical processing methods such as cyanide leaching and amalgamation are used. All equipment is selected based on the deposit, ore type, and mining conditions, ensuring high efficiency, safety, and cost-effectiveness in gold extraction.
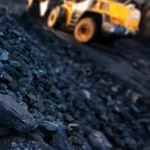
Ore processing equipment plays a key role in the mining industry, ensuring the efficient extraction of valuable components from ore and preparing it for further use.
The first stage is crushing, where jaw, cone, hammer, and impact crushers are used to reduce the size of the ore and make subsequent processing easier. This is followed by milling — with ball, roller, and rod mills providing fine grinding for more precise mineral separation.
Beneficiation is a crucial stage, where gravity and centrifugal concentrators, hydrocyclones, flotation machines, and magnetic separators extract valuable substances from the ore. After that, the ore is sorted using vibrating and drum screens, which separate material into fractions by size.
The next step is smelting: induction and oxidation furnaces are used to extract metals from the concentrate. If necessary, chemical plants — including cyanide and hydrometallurgical units — are used to extract valuable metals through leaching.
To increase productivity at all stages, modern automated control and monitoring systems are implemented, allowing operators to manage the process, reduce costs, and improve processing efficiency.
All this equipment — from crushers to control systems — ensures a high level of valuable component recovery, minimizes losses, and plays a key role in turning ore into a market-ready product.
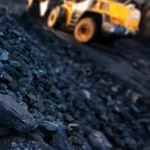
Coal processing equipment is a set of technical tools that ensure the improvement of coal quality and its preparation for further industrial use.
Processing begins with crushing, where jaw, cone, hammer, and impact crushers are used to reduce the size of coal fractions. Next, coal is ground using ball, roller, and rod mills to achieve the required degree of dispersion.
At the beneficiation stage, gravity and centrifugal separators, hydrocyclones, flotation units, and magnetic separators are used — they help remove impurities, increase carbon concentration, and produce higher-quality fuel.
After this, coal is sorted by fraction using vibrating and drum screens. To prepare it for use, coal undergoes drying (in convection, drum, or contact dryers) and, in some cases, thermal treatment, including pyrolysis and coking, which is especially important for metallurgical processes.
Residual waste is processed and disposed of using pneumatic and hydraulic systems, which help reduce environmental impact and utilize secondary resources.
Thus, the full range of equipment at every stage of processing contributes to the efficient use of coal, reduced losses, improved environmental safety, and increased economic efficiency of the coal industry.
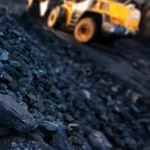
Quarry equipment is an extensive range of machines designed for developing deposits, extracting, transporting, and processing rock materials.
At the initial stages, drilling rigs are used: rotary rigs for blast hole drilling, down-the-hole (pneumatic) rigs for breaking hard rock with compressed air, auger rigs for soft and medium-hard rock, and hydraulic drill jumbos.
After blasting, extraction is carried out using hydraulic excavators, walking excavators, draglines, and mining combines equipped with cutting mechanisms.
For material transportation, heavy-duty mining and quarry dump trucks, belt, pipe, and scraper conveyors, as well as monorail suspension systems, are used.
At the processing stage, jaw, cone, and hammer crushers are used, along with screens for size sorting and flotation units for mineral beneficiation.
Auxiliary equipment includes dust suppression units, ventilation systems, and hydraulic supports to ensure safety in challenging conditions.
Modern quarries actively implement automation: unmanned dump trucks, robotic excavators and drilling rigs, and equipment monitoring systems with sensors and analytics.
All this equipment not only increases production efficiency but also significantly reduces risks for personnel, improves working conditions, and lowers costs at every stage of quarry operations.
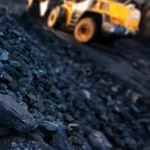
Underground mining equipment is used for extracting mineral resources in underground conditions. It includes machines and systems for drilling, extraction, transportation, processing, and safety.
Drilling rigs create boreholes for subsequent blasting operations. Auger rigs are used in soft rock, rotary rigs in hard rock, and hydraulic drill jumbos increase efficiency in underground settings.
After drilling and blasting, minerals are extracted using mining combines equipped with cutting elements, jackhammers and pneumatic hammers, as well as mobile crushers for primary rock crushing.
Transportation inside mines is carried out with underground dump trucks, belt and scraper conveyors, monorail systems, and mine locomotives. After delivery to the surface, material processing begins. Jaw, cone, and hammer crushers are used for crushing, screens for sorting by size, and flotation units for ore beneficiation.
To ensure safe working conditions, ventilation systems, hydraulic supports, dust suppression systems, and pumps for water drainage are used. Modern mines are also equipped with automated control systems: remote control of machinery reduces risks for personnel, smart monitoring systems track equipment condition, and unmanned machines automate extraction and transportation processes.
Overall, underground mining equipment ensures efficiency and safety at every stage of operation, allowing resources to be used efficiently with minimal risks for personnel and the environment.
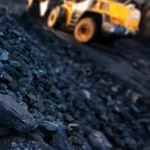
Our services
SUPPLIER SEARCH AND VERIFICATION IN CHINA
Equipment search through partner databases, by countries worldwide, and among industry leaders.
BEST PRICES FOR EQUIPMENT FROM CHINA
Our local representatives will get you the best prices directly from manufacturers.
COUNTERPARTY VERIFICATION IN CHINA
Verification of the company’s registration date, licenses, litigation history, and actual address.
DELIVERY TERMS FROM CHINA
We will deliver your order on the most favorable logistics terms for you (air, rail, or truck).
CONTRACTING
Preparation of export-import contracts: Customs clearance procedures in China and customs clearance in Uzbekistan.
QUALITY CONTROL
Our local representatives control the entire production process of equipment and goods.
LOGISTICS
Supervision of the loading process, providing photo and video reports.
INSTALLATION
Commissioning works and staff training in Uzbekistan.
Our additional services
The main goal of the company Grande is to organize mutually beneficial cooperation between entrepreneurs and companies from around the world and China.
Fast and reliable delivery of goods from China to any destination.
Find a partner for cooperation with China right now.
Reliable purchase of equipment from China with guaranteed quality and reliability.
High-quality verification of Chinese companies before cooperation and investment.
Reliable delivery of goods from China directly to your warehouse.
Wholesale purchase of goods from China on favorable terms.
Directions
The company “Grande” offers an unlimited selection of high-quality, high-tech equipment, machines, installations, and technical tools from leading Chinese manufacturers on a turnkey basis and provides recommendations to its clients on all matters related to purchasing equipment and goods.
We will assist you in selecting agricultural equipment and machinery for growing, harvesting, sorting, and processing fruit and vegetable crops, as well as other types of agricultural production.
Supply of high-quality equipment and belts for food production. Familiarize yourself with the list of main types of machines used in the food industry.
Comprehensive solutions for the light industry from China at affordable prices. Equipment for raw cotton processing, textile printers, weaving machines, textile dyeing equipment, and more.
We offer a wide range of equipment for the production of construction materials. With us, you’ll find machinery for manufacturing paints and varnishes, equipment for producing ceramic materials and products, as well as other types of equipment at the best prices.
Specialized machinery for use in the mining industry, including rock crushing equipment, mineral exploration tools, equipment for extracting mining and chemical raw materials, and other machinery from Chinese manufacturers at the best prices.
We offer innovative equipment for extracting metals from ores or other types of raw materials, as well as technology related to altering the chemical composition, structure, and properties of metal alloys, and the production of various metal products from them.
Turnkey logistics.
Delivery of goods, raw materials, and supplies directly from China to your city.
Entrust your business to professionals
Our company has extensive experience in direct cooperation with Chinese firms. Grande specialists assist businesses daily in purchasing high-quality products from trusted Chinese suppliers. Moreover, Grande will help you with all documentation and ensure delivery of your goods to your warehouse or site.